Understanding Flame Retardant Textiles: Flame Retardant Mechanism And Application
Abstract: This article mainly introduces the combustion mechanism, thermal cracking characteristics, types and mechanisms of flame retardants in flame-retardant textiles, as well as the production methods and testing methods of flame-retardant fibers and fabrics. It covers various aspects from flame retardant principles to production processes, and even testing standards, and looks forward to the future development trend of flame retardant textiles, especially the research and development of low toxicity and low smoke flame retardants and multifunctional flame retardant fabrics. The article also lists some relevant standards and regulations from multiple countries and regions, as well as the flame retardant products and technologies developed by BEGOODTEX company.
1. Development Background of Flame Retardant Fabrics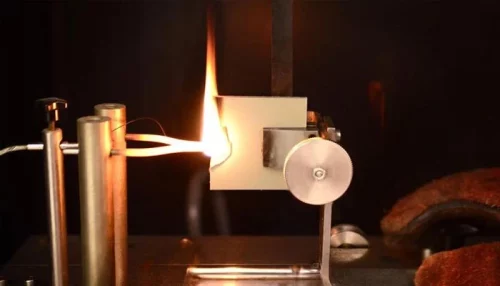
Throughout history fire has been a factor in shaping human progress and development of technology; however it also presents a major threat through the occurrence of fires themselves.The European Flame Retardant Association (FERA) reports that over 5000 individuals lose their lives to fires in Europe with substantial socio economic ramifications.Germany sustains losses of up to 6.5 billion marks due to fires while the economic impact of fires, within the European Union represents 1% of the regions GDP. In China each year sees an average of 30 000 to 40 000 fire incidents leading to 2 000 to 3 000 fatalities and economic losses ranging from 200 million to 300 million yuan that are increasing over times.
Flame retardant technology had its early roots back in the nineteen thirties initially with non permanent treatments before progressing to the use of longer lasting flame retardant materials, like those used in military tents during World War II. During the 1960s era nations like Europe the United States, and Japan each created flame guidelines, for textiles mandating certain locations and products to utilize flame retardant materials.
2. Importance of Flame Retardant Fabrics
Flame retardancy refers to the property of a material that can slow down or prevent combustion, which can be inherent or achieved through post-processing. The mechanism of action of flame-retardant textiles is to prevent chain reactions during the combustion process, such as heat absorption, changing the thermal degradation mode, and reducing the production of combustible gases, in order to achieve flame-retardant effects.
Research has shown that flame-retardant fabrics can significantly improve safety. For example, compared to untreated fabrics, flame-retardant fabrics can extend escape time by 10 to 15 times, reduce the heat and toxic gases released during combustion, and avoid the production of thick smoke.
3. Regulations on Flame Retardant Fabric Combustion Technology
Currently, in the world of textiles, testing for flame retardancy involves methods internationally recognized by different countries, such as the UK’s BS standard, Germany’s DlN standard, Canada’s GCSB standard, the US’s FS standard, Japan’s JlS standard, France’s ANF standard, Sweden’s SlS standard, China’s GB standard, and international standards by lSO. Different areas and institutions in nations like well-known urban centers or states such as New York and California in the USA as well as departments like Commerce (DOCFF), Transportation (DOT), and military organizations have their own unique testing standards and methodologies that are followed by various groups or associations like the National Fire Protection Association (NFPA) the Association of Textile Chemists and Dyers (AATCC) the Society, for Testing and Materials (ASTM) among others.
United States
Since 1953,the United States has enacted the Flammable Fabrics Act (FFAP) which mandates that textiles adhere to flammability technical requirements.Some associated standards include;
- NFPA 701: A fire testing standard for textiles and film materials developed by the National Fire Protection Association, primarily testing the combustion characteristics of materials when exposed to flames.
- NFPA 2112 focuses on the guidelines for flame apparel in industrial settings like the oil and gas sector where protective clothing is crucial for shielding against brief bursts of intense heat, from flames.
- CFR 1615/1616: Federal regulations set out fire safety standards for kids pajamas, in America by detailing what materials can be used and how fast flames can spread on them.
Canada
Canada has passed the Hazardous Products Regulations and related regulations (such as children’s sleepwear, carpets, tents, etc.), which are implemented by Health Canada to ensure that all textiles meet flame retardant requirements. Partial related standards:
- CAN/ULC-S102: Fire testing methods for building materials and components, including home decor.
- CAN/CGSB 4.2 No. 27.5: Burning performance of bedding.
Japan
Japan does not have specific flame retardant requirements for clothing products, but has established flame retardant standards for carpets and curtains in buildings, requiring textiles used in specific locations to meet the prescribed flame retardant performance and be labeled with “fire prevention labels”. For example, JIS L 1091 applies to household textiles (curtains, bed sheets).
Australia
Each state in Australia has different technical regulations, with Western Australia enacting the Fair Trade Act 1987 and the Children’s Evening Dress Standards 1988; Tasmania has the Flammable Clothing Act 1973 and the Flammable Clothing Regulations 2002; New South Wales has enacted the Fair Trade (General Requirements) Regulations 2002. These regulations stipulate that the flame retardancy and testing methods for children’s evening wear (such as pajamas, bathrobes, etc.) numbered 00-14 must comply with the AS/NZS 1249 standard.
UK
The United Kingdom has rules regarding flame retardant safety for evening attire. Back in 1985 the Evening Wear (Safety Regulations came into effect as a replacement for the Womens Sleepwear (Safety Regulations). In 1987 there were amendments made extending these regulations to cover all types of evening wear. According to these regulations childrens evening wear for ages ranging from 3 months, to 13 years must adhere to the standard BS5722 and should have a permanent label specifying if it meets the combustion standard. Evening attire that has been treated with flame chemicals should come with labels warning about wash instructions and the specific detergents to use for cleaning purposes as per the guidelines outlined in BS5651 before conducting any tests or assessments, on its properties. Partial list of standards;
- BS5815 is predominantly employed to assess the fire resistance of furniture to guarantee that materials offer safety in case of a fire outbreak.
- BS5852 CRIB 5 is a testing standard that assesses the fire resistance of furniture and filling materials at a level of fire safety requirements.
- BS5867 TYPE C is a fire resistance standard specifically designed for curtains and interior decorative fabrics; a Type C rating signifies that the material demonstrates fire resistance when exposed to flames.
- BS7175 Source 7: Evaluating the fire resistance of bedding, Source 7 is a high standard fire protection requirement commonly used for bedding in public places.
4. Thermal Decomposition of Textiles
The burning of fabrics is influenced by their type, structure and composition. Can be categorized into various groups such as non flammable fire resistant fire retardant, flammable and combustible. The process of burning requires three elements; a source of heat, oxygen and flammable materials. Fabrics ignite due, to sources of heat. Once the temperature of the heat source reaches a level the fibers start to break down and release flammable gases that combine with oxygen and catch fire. The burning of fabrics involves stages like warming up the material first before it melts and cracks open to decompose and eventually catch fire due to oxidation.
Types of fibers | Name of fiber | Close to the flame | In the flames | Leave the flame | Residual form |
Cellulose fiber | Bamboo pulp fiber | Non-melting and non-shrinking | Burn quickly | Keep burning | A small amount of soft dark gray |
Bamboo fiber | Non-melting and non-shrinking | Burn quickly | Keep burning | .A small amount of soft gray | |
Adhesive | Non-melting and non-shrinking | Burn quickly | Keep burning | A small amount of soft grayish-white gray | |
Cotton and kapok | Non-melting and non-shrinking | Burn quickly | Keep burning | A small amount of soft gray-black gray | |
Flax | Non-melting and non-shrinking | Burn quickly | Keep burning | A small amount of silk strip-shaped gray-white gray | |
.Protein fiber | Soy protein fiber | Contract | There is black smoke in the burning. | Keep burning | Crispy black and gray, a small amount of hard pieces |
Milk protein fiber | Melt and curl | Curl, melt, burn | Burning, sometimes self-destructing | Black, basically crispy, | |
Shell cord fiber | Non-melting and non-shrinking | Burn quickly, do not melt and keep the original circle bundle. | Keep burning | .Black and gray, fragile | |
Wool, silk | Contraction or curling | Gradually burn | Not easy to burn | Crispy black gray | |
Synthetic fibre | Polyester fibre | Contraction, melting | Melt first and then burn | There is a lot of black smoke, and there are molten liquid dripping, | Glassy, dark brown hard ball |
The melt drops are dark brown. | |||||
Polyamide fibre | Contraction, melting | Melt first and then burn | .There are melt drips, and the melt drops are brown. | Glassy, dark brown hard ball | |
Acrylic fibres | Contraction, micro-melting, scorching | Melting combustion | There are small glowing sparks. | Crispy, black hard pieces | |
Polyvinyl alcohol fibre | Contraction, melting | Burning | Continue to burn | Crispy, black hard pieces | |
Polypropylene fibre | Slow contraction | Melting combustion | There are melt drops, and the melt drops are milky white. | Hard yellow-brown ball |
Cellulosic Fibers
Cellulose fiber is a material that changes when heated and can result in solid remnants as well as liquids and combustible gases being released. The way in which the fiber breaks down under heat determines if it will keep burning or not. When cellulose burns down it goes through two types of combustion. One with flames and the other without (smoldering).
The breakdown process can be seen in three stages:
1.The initial breakdown happens at temperatures below 370 ℃
2.The main breakdown occurs between 370 ℃ to 430 ℃
3.The final breakdown stage happens above 430 ℃
At the cracking phase (with temperatures surpassing 430 ℃) the combustion performance is dictated by the cracking products, research findings indicate that diminishing the production of flammable elements can effectively lower combustion hazards. For instance; During pyrolysis processes of cotton fibers approximately 28 flammable substances are generated; conversely with flame retardant treated cotton fibers the types and quantities of pyrolysis products are notably reduced.
Polyester Fibers
The way polyester fiber burns is like how other synthetic polymer materials burn as well. When polyester fibers are exposed to heat they break down. Give off flammable gases that help the fire spread faster. To prevent the fire from spreading it’s important to minimize the release of these gases, during decomposition slow down the reactions happening in the air soak up the heat produced by the fire or limit how long the fire lasts by cutting off oxygen from the environment.
Explore more details on How Flame Retardant Technology Applied In Polyester Fabric. by clicking here for more information.
5. Understanding Flame Retardants Mechanisms
Flame Retardant Mechanisms in Textiles
- Melting theory (surface coverage theory)
Some substances, such as borax and boric acid, melt and form a glassy film covering the surface of fibers when heated, isolating air and suppressing combustion. Phosphides can promote carbonization, while bromides decompose to produce non combustible gases, further isolating air or diluting combustible gases, thereby producing flame retardant effects.
- Heat absorption effect
Flame retardants reduce the temperature of polymer surfaces and combustion zones through heat absorption, dehydration, phase change, or decomposition, thereby slowing down the thermal decomposition process.
- Dehydration theory
Phosphorus based flame retardants generate pyrophosphate upon contact with flames, which has a strong dehydration effect and helps to carbonize fibers. The formed carbonized film can effectively isolate air and reduce the release of flammable gases.
- Condensed phase flame retardant
The flame retardant effect of condensed phase is achieved by delaying or interrupting the thermal decomposition process of materials, and common methods include:
- Flame retardants delay or prevent the thermal decomposition of flammable gases and free radicals in the solid phase.
- The use of inorganic fillers makes it difficult for the material to reach the thermal decomposition temperature through heat storage and conduction.
- Flame retardants decompose and absorb heat when heated, slowing down the temperature rise.
- The surface of flame-retardant materials forms a porous carbon layer, which provides insulation and oxygen barrier, preventing flammable gases from entering the gas phase and interrupting combustion.
- Gas phase flame retardant
Gas phase flame retardancy suppresses gas-phase combustion reactions by capturing and eliminating free radicals such as H · and HO ·, effectively controlling the combustion process.
- Dust particles or wall effects
Free radicals may lose their activity when in contact with dust particles or vessel walls, reducing the rate of gas-phase reactions and thus inhibiting combustion.
- Droplet effect
When thermoplastic fibers are heated, they melt, which decreases their surface area in contact with air and can lead to droplets detaching from the flame, thus lowering the rate of combustion. To optimize flame retardancy, various mechanisms typically collaborate through synergistic interactions to enhance the overall flame-retardant performance.
Principles of Various Flame Retardants
There are various types of flame retardants, mainly divided into halogen flame retardants, phosphate flame retardants, inorganic flame retardants, and expansion flame retardants. The flame retardant mechanism of each type of flame retardant is different.
- Flame retardant mechanism of halogenated flame retardants
Upon heating halogen flame retardants decompose and produce non combustible gases, in most cases an hydrogen halide that get to the surface of material covering it with a blanket which isolates oxygen from combustion reaction. Both hydrogen halides and free radicals combine to form low activity chlorine or bromine radicals which further lowers the combustion rate.
- Flame retardant mechanism of inorganic phosphates
Phosphorus flame retardants act by the mechanism of dehydration and carbonization. Phosphates are able to form polyphosphate glass bodies at high temperatures, which encase the material and prevent oxygen from reaching its surface and supporting combustion. Ion pairs can also improve the flame retardant effect when combined with metal phosphates and chlorides.
- Flame retardant mechanism of phosphate ester flame retardants
Phosphate ester fire retardants mitigate the flammability of materials by forming non-volatile phosphoric and metaphosphoric acids that catalyze dehydration, as well as an insulating carbon protection layer.
- Synergistic effect of antimony trioxide and halogenated flame retardants
Antimony trioxide and halogen flame retardants can work together to absorb heat, consume free radicals that form during combustion of the resin, reduce surface temperature or flammable gas release rate in separation fire stage one side,optimize synergist effect on another direction.
- Flame retardant mechanism of phosphorus nitrogen flame retardants
Phosphorus/Nitrogen Flame Retardant Will Generate The Carbonized Foam Layer By Expansion As Well, Such Content Of Last One Features Are Just About Heat Insulation, Oxygen And Smoke Disconnection And Molten Drops Preclusion. The foam carbon layer, as a kind of porous material produced by the polyurethane rigid foams can isolate and prevent the source from firing, It will inherently slow down combustion to overcome this problem.
6. Production Pathways for Flame Retardant Fabrics
There are essentially two approaches to making fibers and textiles flame retardant. Modifying the fibers themselves for permanent flame resistance or using flame retardant finishes on the surface of the material. When it comes to fibers like cotton wool and linen, post-finishing methods are employed for flame retardancy by either adsorption deposition or chemical bonding to fix the flame retardant, on the fabric or yarn ensuring it provides flame-resistant properties. Synthetic fibers like polyester and acrylic may have flame retardants incorporated during spinning. Then altered through copolymerization or blending to enhance their flame retardant properties. Alternatively flame retardancy in fibers could be achieved through post finishing treatments for added fire resistance. Compared to the methods applying flame retardants after manufacturing is simpler requires less investment and yields quicker outcomes, which makes it a more feasible option, for introducing new product lines. Post processing techniques can influence the fabrics strength and appearance well as affect its flame retardant properties compared to the untreated silk fabric modification.
Production Pathways for Flame Retardant Fibers
Flame retardant fibers obtain flame retardant properties by directly adding flame retardants during the fiber production process. The methods mainly include copolymerization, blending, graft copolymerization, flame retardant absorption, fiber surface halogenation, and post finishing.
- Co polymerization: Addition of compounds containing flame retardant elements (phosphorus, halogen, sulfur, etc.) as co monomer of the polymer chains to improve fiber flame retardancy. This method has the advantages of long-lasting flame retardancy of the fiber, but the high temperature polymerization temperature would cause side reactions and be detrimental to the performance of the polymer.
- Blending method: This method involves adding flame retardant at the melt (mixture of fibers in the molten state.) This necessitates flame retardants to undergo thermal stability, polymer compatibility, and non-non-performance to fibers. It needs high-temperature flame retardants that can get along with polymers and will not affect the performance of fibers.
- Grafting copolymerization: Compounds with phosphorus and halogen is grafted onto the molecular chains of the fibers using chemical methods or high energy radiation to improve flame retarded [9–12]. Grafting copolymerization: Phosphorus and halogen compounds are grafted onto the molecular chains of fibers using chemical methods or high-energy radiation for enhanced flame retardancy.
- Flame retardant absorption method: adsorbing flame retardants onto fibers, which is simple but less effective.
- Halogenation of fiber surface: By radiation-induced chlorination treatment, the fiber surface obtains flame retardancy.
- Post finishing method: Apply flame retardant evenly on the surface of fibers or fabrics. This method is simple and easy to implement, but the flame retardant effect is not long-lasting and can affect the texture and color of the fabric.
Production Pathways for Flame Retardant Fabrics
Flame retardant fabrics are usually made by post finishing the fabric surface and applying different finishing methods to make the fibers flame-retardant. Common flame retardant finishing methods include padding and baking, exhaustion dyeing, coating, spray, etc.
- Dip rolling baking method: The most common method of flame retardant finishing, soaking flame retardants, drying and baking. The same bath as the rest of finishing methods (i.e., soft finishing) can be done in. Can be done in the same bath of finishing process (like Soft finishing)
- Exhaustive dyeing method: The fabric is soaked in a flame retardant solution and then dried. It is suitable for hydrophobic synthetic fibers and is usually dyed in the same bath. This method has poor flame retardant effect.
- Coating method: Mix flame retardants with crosslinking agents or adhesives and apply them to fabrics. Common coating methods include scraper coating, casting coating, and rolling coating.
- Spray method:It is used for heavy fabrics area, the equipment is not suitable for general finishing equipment, manually or mechanical spray flame-retardant finishing. Spray type: it is suitable for heavy fabrics that are not suitable for traditional finishing equipment. Flame retardant finishing is carried out by manual or mechanical spray.
Methods for Flame Retardant Finishing of Different Fiber Fabrics
- Polyester fiber. Polyester is a flammable material that is treated in a flame retardant manner through copolymerization, blending, composite spinning and post finishing methods. The flame retardance with copolymerization method is superior, but expensive; while with the blending method, the process is simple and economical, but the flame retardant effect is relatively poor at the same time of flame retardance with copolymerization, this is because that the blending method lacks the synergistic effect of flame retardant and polymer.
- Nitrile chlorinated fiber: As a bonded flame-retardant fiber by means of copolymerization methods with blending (copolymer) method. A good flame retardant fibers is prepared from the copolymerization of monomers containing chlorine (for example, vinylidene chloride with acrylonitrile) As in the case of example copolymerization of chlorinated monomers such as vinylidene chloride with acrylonitrile, better flame-retardant functionalities are incorporated into the fibers.
- Cotton fabric:It is primarily an easy catching fire fabric, some flame retarding finishing is necessary. There are two kinds of flame retardant finishing: one is non capable (take phosphate, ammonium chloride and other methods as example) and the other is capable finishing (for example: tetra hydroxymethyl phosphate chloride are fire retardants). incorporate a flame retardant finishing.
- Wool fabric: Wool itself has a relatively high flame retardancy, but when higher flame retardancy performance is required, flame retardant finishing needs to be carried out. Conventional technology applies the finish as complexes and/or free complexes of titanium, zirconium or hydroxy acids to increase the flame retardancy at almost no change of hand of wool. Typical wool finishes are titanium and zirconium muds or hydroxy acids that form complexes with fiber and enhance the level of flame retardancy without changing the feel of the wool.
- Hemp fabrics: Cellulose (a carbohydrate polymer that makes up the bulk of hemp fibers) is highly combustible and ignites rapidly. Meanwhile, the hemp fiber has the lowest crack temperature so it is essential to treat the hails of phosphorus containing flame retardants and obtain the flame retardant effect by increasing the temperature of carbonization and decreasing the generation of combustible gases. Hemp Fabrics: Hemp fibre which be spinnable on textile is burning nature and easily break because of low cracking temperature, phosphorus containing flame retardants is common used in order to promote the carbonization process and the release of ash to reduce flame and combustible gases to achieve flame-retardant effect.
- Nylon fabric: Flame retardant finishing of nylon fabric is more complicated than cotton fabric, and preferred flame retardants are sulfur-containing flame retardants such as thiourea and ammonium thiocyanate which have high flame retardant effects on nylon. Nylon fabric Flame retardant finishing of nylon fabric are more complex, sulfur-containing flame retardants such as thiourea and ammonium thiocyanate have good flame retardant effect on it.
- Polyester / cotton blended fabric: The flame retardant finishing of polyester cotton blended fabric is more difficult, to be the attribution to the characteristics of the two fibers are different. Each needs different flame retardant treatment, and complementary flame retardants reinforced. The flame retardant treatment is usually required for each of the components though this can be done using synergistic flame retardants.
7. Methods for Testing Flame Retardant Fabrics
Limiting Oxygen Index (LOI) Method
This technique identifies the minimum oxygen concentration required for fabrics to ignite in a blend of oxygen and nitrogen gases. A higher LOl value indicates flame retardant properties. While this approach is valuable, for investigations it is not widely utilized in everyday manufacturing practices.
Vertical Burning Method
Assess the effectiveness of flame properties by examining how fabrics burn and how long it takes for them to ignite and the extent of damage caused under particular flame settings.This approach is commonly employed to test a range of fire fabrics and is particularly prevalent, in Chinese standards where it plays a significant role.
45° Incline Burning Method
Assess how well the fabric resists flames by measuring how long it burns for and the size of the damage area when placed at a 45 degree angle.
Surface Burning Method
Lets test the fabrics fire resistance by measuring how and for how long the flame spreads on a flat surface.
8. Development Trends of Flame Retardant Fabrics
The Current Status of Global Flame Retardant Textiles
In the few years there have been notable advancements in global flame retardant technology for textiles. Various research organizations and businesses have been working on materials and methods to improve flame retardancy such as polypropylene flame retardant masterbatch and composite solutions that offer both flame retardant and anti static properties. The main focus of the research project is on developing high performance flame retardant fibers and exploring their usage specifically looking at fibers with high flame retardant properties and their use in blended fabrics. These fibers have an oxygen index ranging from 45 to 50.
Various nations have also created a range of flame retardants, with exceptional fireproof qualities concurrently. For instance, BEGOODTEX has developed Aquafyreguad™, a line of flame retardants designed for different types of natural and synthetic fibers.
Development Trends of Flame Retardant Textiles
- Strengthen the development of flame-retardant fibers
Flame retardant fibers have low production and application, and more high-performance and multifunctional flame-retardant fibers should be developed in the future as they can be used in special industries such as the military and firefighting. The yield of flame-retardant fiber and the extent of application are low, and in the future, a great deal of research and production work must be done on flame-retardant fiber research, development and production work, the high performance and high-function flame-retardant fiber particularly small number of special technology including the task of the military and fight flame field prospect.
- Multi functional research
Currently, most of the flame-retardant textiles can only play the flame-retardant function. BEGOODTEX company of China has announced flame-retardant multifunctional fabrics, like: Flame retardant & Antibacterial (FRANtiBact ™), Flame retardant & Waterproof (FRANTiAqua ™), Flame retardant GRS (GRSFRTex ™), Flame retardant & UV resistant (FRANTIUV ™), and Flame retardant & Light block (AntiLightFR ™), Flame retardant & anti-static (FRStaticGuard ™), Flame retardant & medical grade (FRMediGuard ™).
- Research and development of low toxicity and low smoke flame retardants
The future trend is to develop flame retardants with low toxicity, low smoke, and pollution-free. Recently BEGOODTEX has launched ECO natural fibres like FR 100% Cotton and FR 100% Viscose which are eco-friendly, biodegradable, formaldehyde free, chemical free, non-irritating and non-allergenic. ECO natural fibers like FR 100% Cotton and FR 100% Viscose have recently been introduced by BEGOODTEX and are environmentally friendly, biodegradable, formaldehyde free, chemical free, non irritating and non fatiguing.